Abstract
Custom design and manufacturing projects require careful planning, precise execution, and a keen eye for detail with a bit of creativity sprinkled on top. In the realm of babbitt bearings for the hydroelectric industry, this process becomes even more critical. In this case study, we will take you through the steps involved in our company’s approach to a custom design and manufacturing job. From the initial site visit to the final commissioning, we leave no stone unturned to ensure the highest quality and reliability for our clients.
Context
New issues can arise when you demand more from your machine than it can handle. A 100-year-old double overhung Pelton hydroelectric unit suffered continuous bearing wipes due to extreme shaft bending and misalignment. Pioneer analyzed the issue and designed and manufactured an entirely new bearing system—a pair of 25” diameter pivoted journal/thrust bearings. Pioneer’s turn-key upgrade now allows this hydroelectric unit to produce reliable clean power at its full potential. This is just one project of a plethora of hydro related solutions we’ve provided.
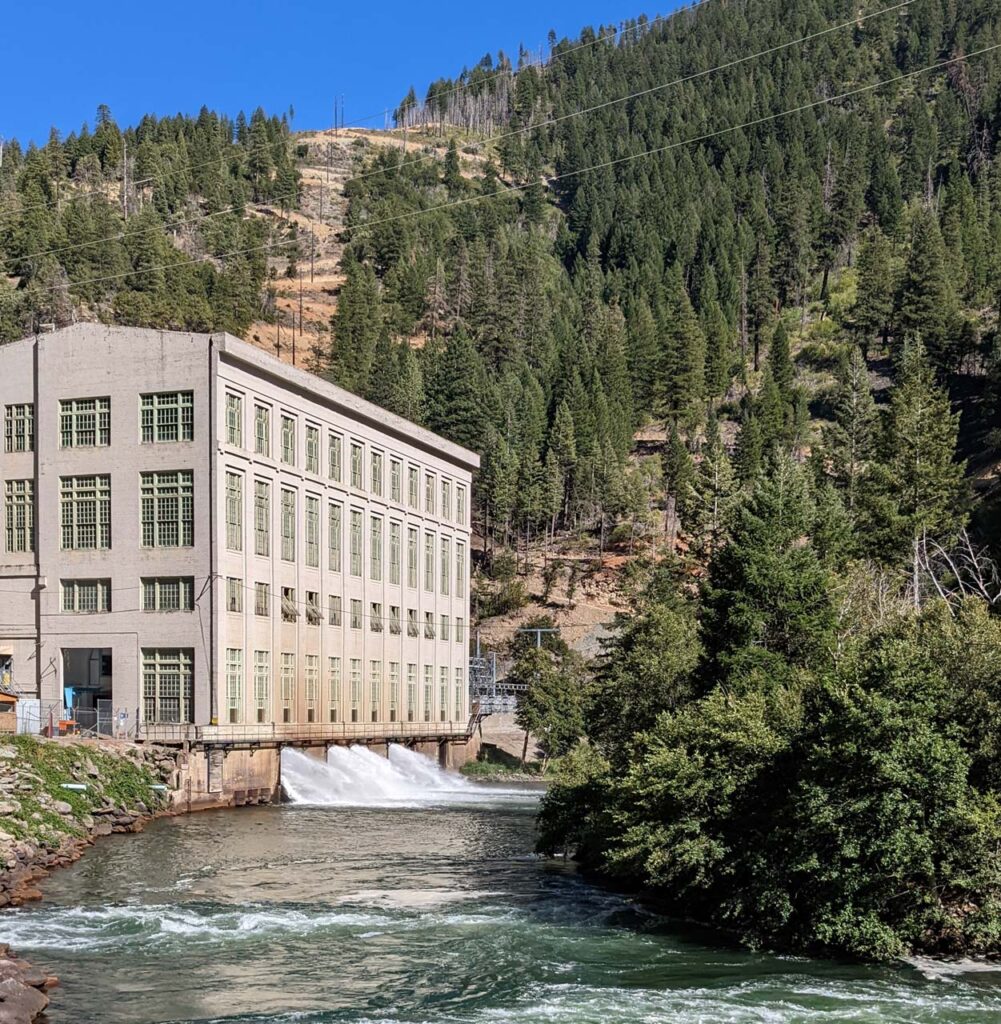
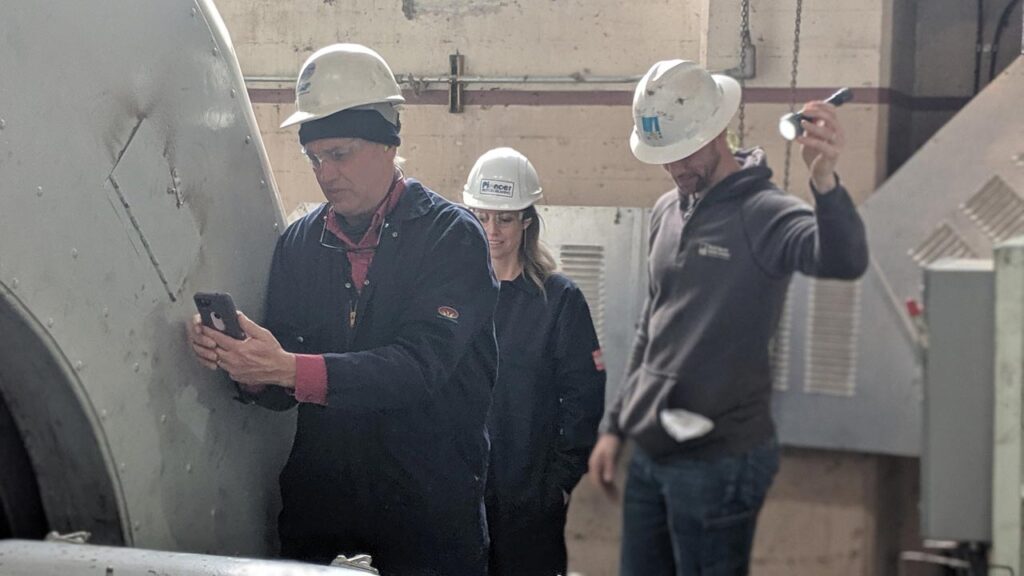
The Initial Site Visit
Ideally, every major project begins with an in-person visit to the site. This crucial step allows our team to understand the specific requirements, challenges, and unique environmental factors associated with the installation. By conducting a thorough assessment, we gather essential information, including measurements, photos & video, that shape the subsequent stages of the project. With a long history of traveling to customer sites, it was another routine effort to send multiple personnel on-site. When there is a systemic bearing issue, it’s always best to see the situation first hand to fully understand the problem.
Manufacturing
Once the design is approved, we begin the manufacturing process. It starts with the raw forging being cast with a small layer of babbitt/ Our skilled machinists work meticulously to machine the babbitt bearings with precision and attention to detail. We utilize state-of-the-art machinery and follow strict quality control protocols to ensure that each component meets our rigorous standards.
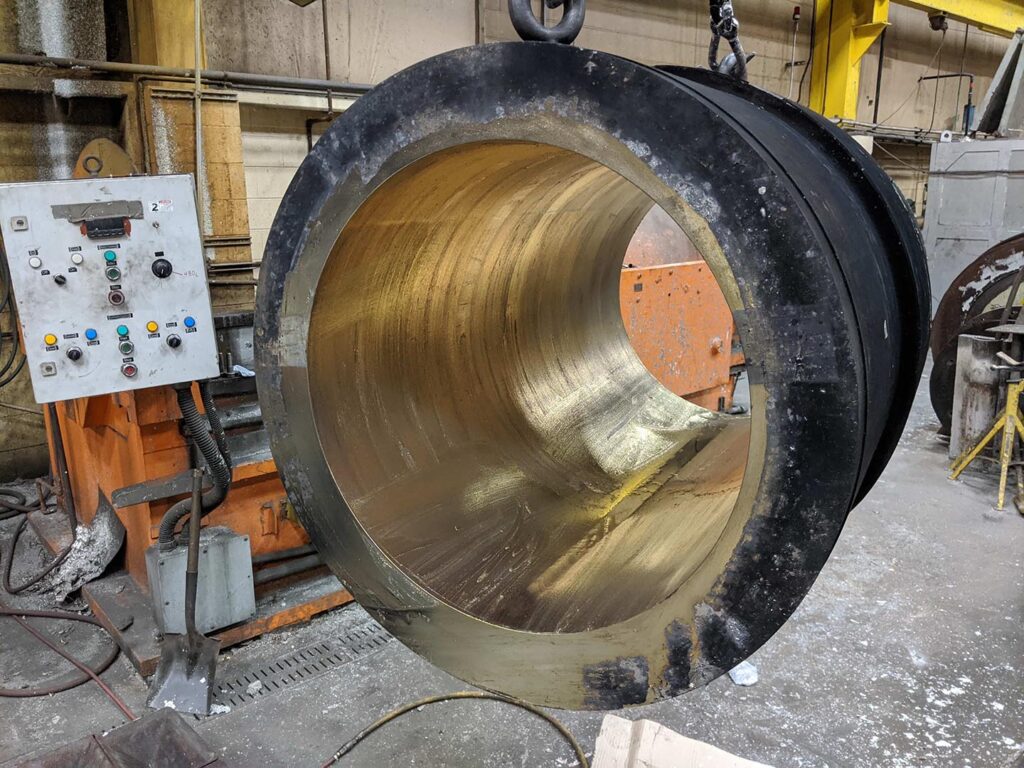
Installation Support
With the completion of the manufacturing component finished and the FAT signed off on, Pioneer then traveled back to the customer site some 2.5 years after the initial inquiry. Pioneer provided oversight on and training on the installation of the new bearing system. The installation was so unique that our design engineer invented a new slip-in harness/carriage system to delicately rotate in the slinger ring lower halves.
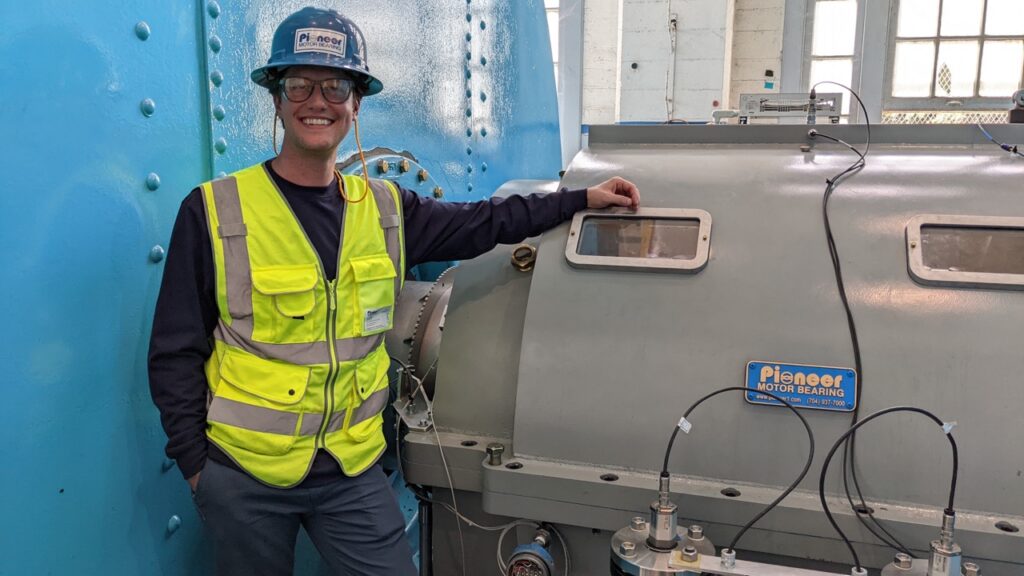
Conclusion
The journey of a custom babbitt bearing design and manufacturing job encompasses several crucial steps, each essential to delivering a high-quality product. From the initial site visit to the final commissioning, our company remains committed to excellence and customer satisfaction. By employing a meticulous approach, leveraging advanced technology, and collaborating closely with our clients, we ensure that our babbitt bearings meet the highest standards of performance and reliability in the hydroelectric industry. This particular 100-year-old hydro plant looks like it’ll have another successful century of clean power generation.
If you have problems with your hydro thrust or journal/guide bearings please reach out to us so we can help solve your problems.

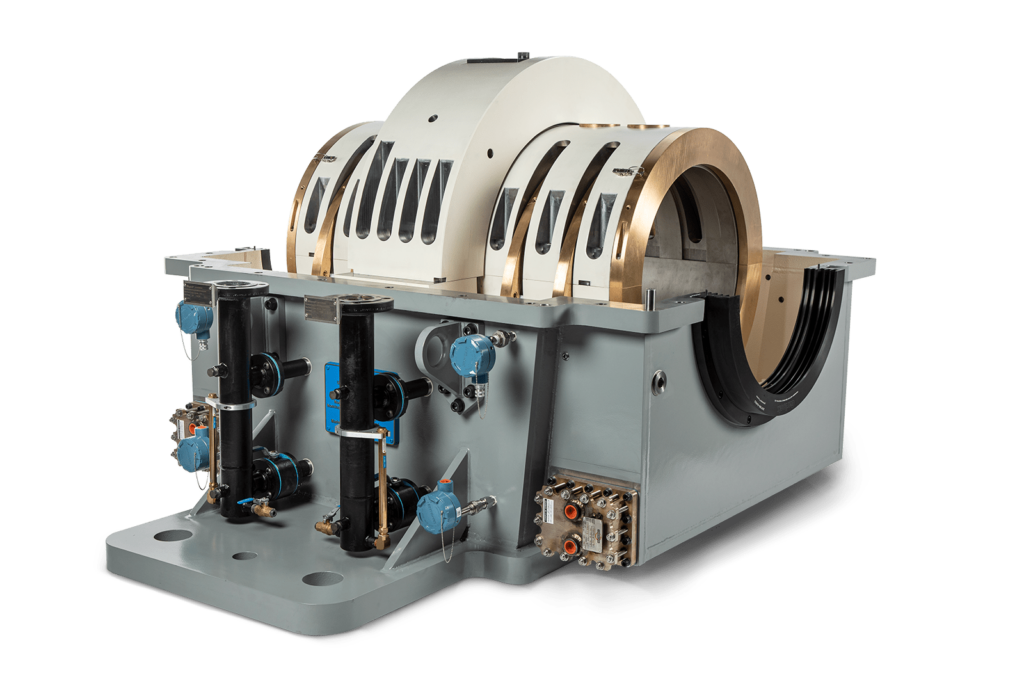